Ouroboros leads the way in sustainable public art
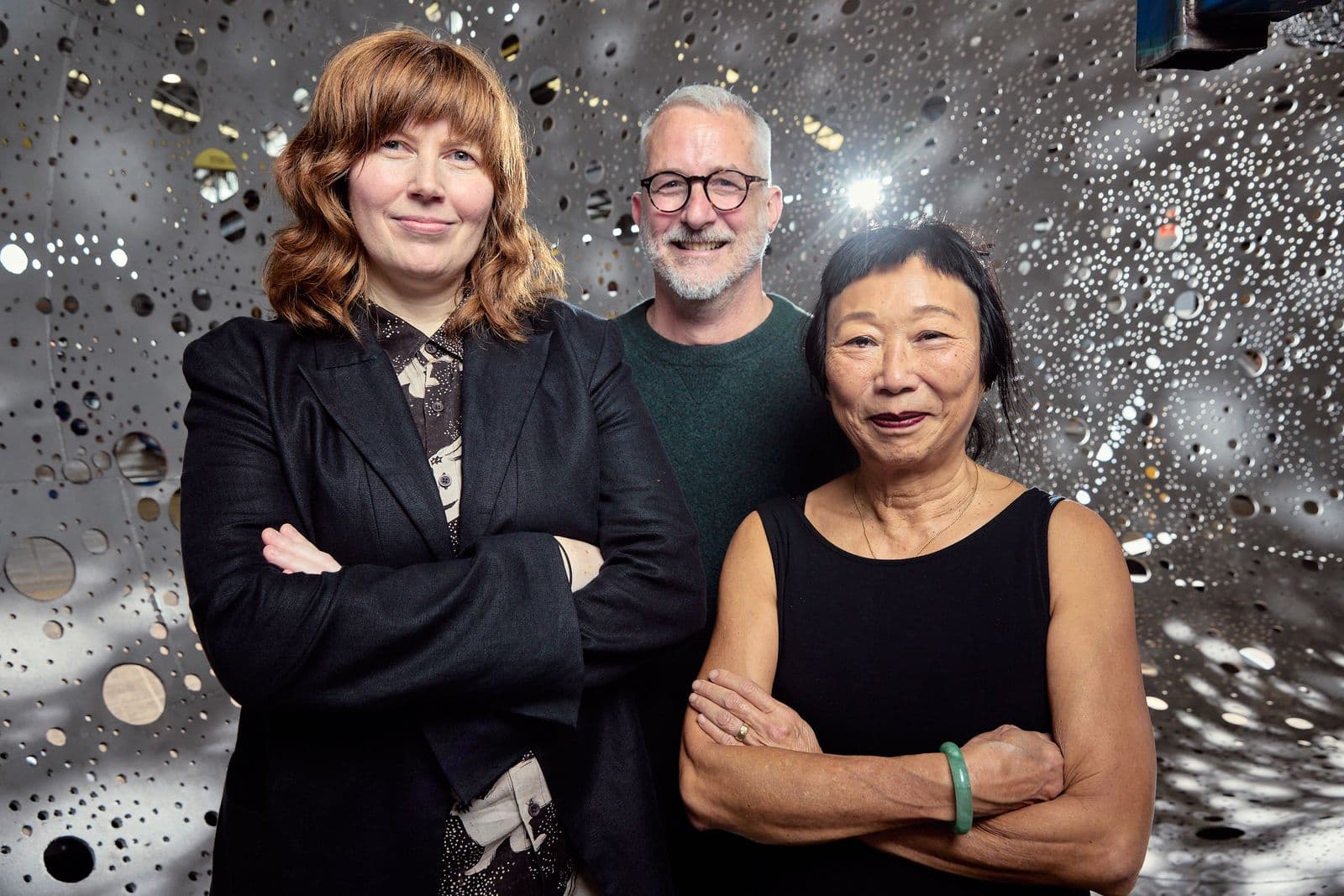
Amanda Harris, Daniel Tobin and Lindy Lee inside Ouroboros at UAP | Urban Art Projects, Brisbane, 2024, National Gallery of Australia, Kamberri/Canberra, photo: Josef Ruckli
When the National Gallery commissioned LINDY LEE to create her first immersive public sculpture, it gave both parties and Brisbane fabricator URBAN ART PROJECTS (UAP) a unique opportunity to set a new sustainability standard for large-scale public art in Australia.
Lindy Lee’s forthcoming Ouroboros 2024 enjoys the distinction of being the contemporary Australian artist’s first foray into immersive public sculpture – art you can actually enter and explore from the inside out.
Commissioned to celebrate the National Gallery’s 40th anniversary, Ouroboros is also the first of a number of new works that will activate the National Sculpture Garden and surrounds, set to be revitalised and transformed over the coming years.
Yet what makes Ouroboros truly remarkable is the sustainable way it was made, an approach championed from the outset by Lee, the Gallery and UAP.
Ouroboros is the first work of art fabricated by UAP to come with a full ingredients list – similar to what you see on the side of a cereal packet – including a calculation of carbon emissions required to produce it.
'This is a significant work with a lot of tonnage of materials in it,' says Amanda Harris, General Manager, UAP Australia, who has overseen the three-year project. 'Our mindset was, if we’re going to put this out there in the world, how do we do that in as low-impact a way as possible?'
That’s no small feat for a walk-in sculpture with a total surface area of 150 square metres, comprising 270 panels of 10mm-thick, mirror-polished stainless steel, welded to form a self-supporting structure weighing 14 tonnes, into which 45,000 holes have been perforated by hand in six different sizes, ranging from 16mm to 140mm in diameter, using a plasma cutter.
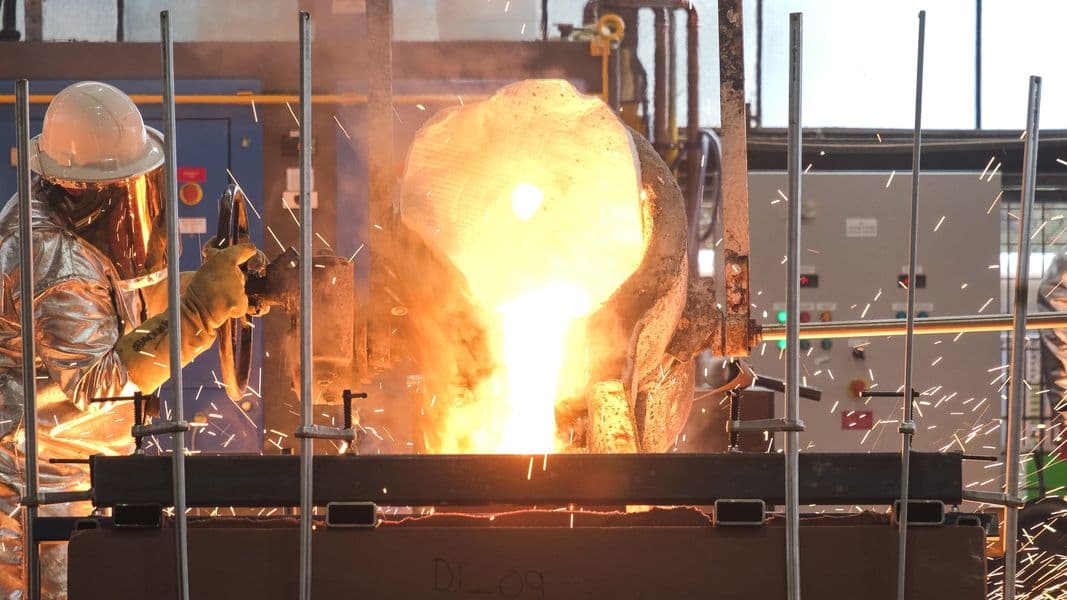
Molten stainless steel being poured into a sand mould for Ouroboros at UAP | Urban Art Projects, Brisbane, 2023, National Gallery of Australia, Kamberri/Canberra, photo: Josef Ruckli
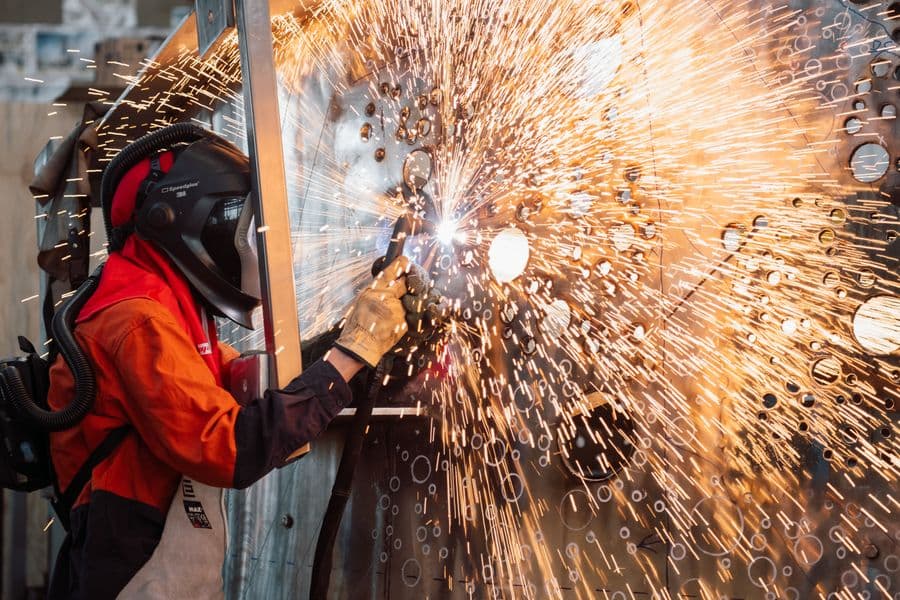
Plasma cutting of Ouroboros, Brisbane, 2022, courtesy of UAP | Urban Art Projects
Ouroboros at UAP | Urban Art Projects, Brisbane, 2023, National Gallery of Australia, Kamberri/Canberra, photo: Josef Ruckli
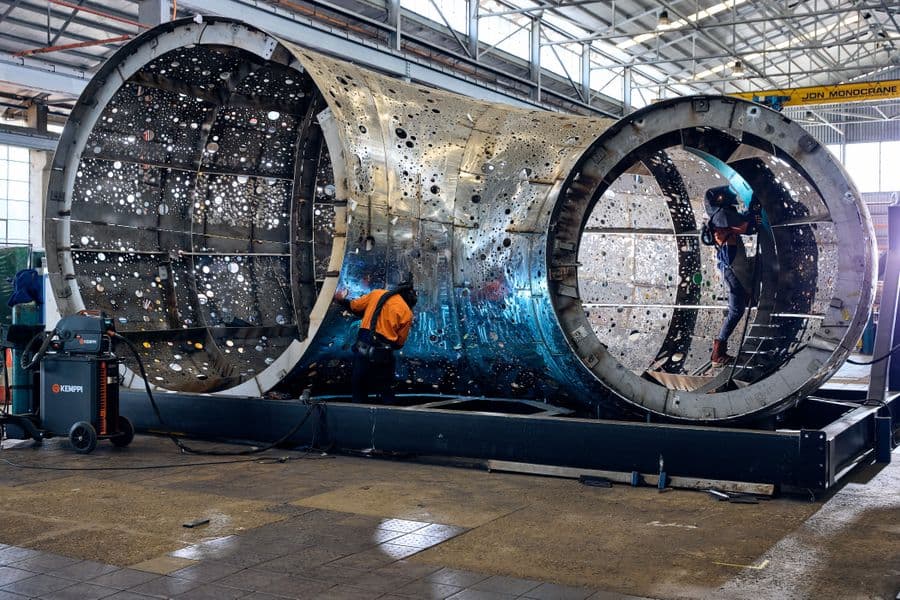
Ouroboros at UAP | Urban Art Projects, Brisbane, 2023, National Gallery of Australia, Kamberri/Canberra, photo: Josef Ruckli
Fortunately, UAP has the capacity to make stainless steel – an alloy composed primarily of Iron, Chromium and Nickel, with smaller amounts of Molybdenum, Manganese, Silicon and other metals – from 100 per cent recycled scrap metal.
'That represents around a 70 per cent reduction in carbon emissions on the raw materials input, based on virgin versus recycled stainless steel, so there was a huge saving right there,' says Gilbert Guaring, Global Head of Marketing, Sustainability and Engagement, UAP.
And knowing the project was coming up, UAP was able to secure a Made in Queensland grant to upgrade its foundry from an older gas model to an induction furnace, partly powered by solar energy.
'What used to take four hours or more to heat up a batch of metal, depending on the material and how full it is, now takes less than an hour,' says Harris.
The project has also triggered a change in the way UAP works with sand moulds, which are traditionally used to cast panels – stainless steel or otherwise – by pouring molten metal into them straight from the furnace.
'Sand is one of our biggest waste products, so we’re moving over to recycled sand and will be recycling 75 per cent of it in the future,' says Harris. 'We are still commissioning the machinery required to do that, so we couldn’t use recycled sand for Ouroboros, but it was the catalyst for change.'
Another win for efficiency is that the work has been designed so that it can be transported by road from Brisbane to Canberra in its finished form, ready to be integrated with the water feature and landscaping elements, preparation of which is already underway.
'From a sustainability angle, it’s better to transport it whole,' explains Harris. 'If we couldn’t, we’d be flying down additional specialist team members, as well as tooling and consumables, to actually do the final parts of the fabrication onsite, which costs more and has greater impact.'
Once Ouroboros has been delivered to the Gallery, UAP will run the numbers to determine total carbon emissions.
'We used a spectrometer for every batch of metal undertaken for this project, so we have records of the exact composition of the steel,' says Harris. 'We also tracked labour involved and cross-referenced that with the machinery employed for different tasks – for example, the two kilometres worth of welding that’s been required to join the panels together.'
'Transportation and packaging are also part of the equation,' adds Guaring.
'And the planned transportation route might change at the last minute due to bad weather or an unforeseen road closure,' says Harris. 'Hence, why we do the calculations at the end.'
At its core, Ouroboros is a work of art about infinity that can itself enjoy an endless life cycle.
'There’s a lot of talk about 'cradle to grave' when it comes to calculating carbon emissions,' says Guaring. 'But what we’re doing with Ouroboros is actually 'cradle to cradle'. If it’s decommissioned in a hundred years, there is the opportunity for it to be recycled.'
'Should the stainless steel ever need to change form, it can, because it’s not contaminated,' says Harris. 'It’s got a long-term path to a circular life cycle.'
Building on the National Gallery’s Environmental Sustainability Action Plan 2022-25, Ouroboros has also helped shape UAP’s own commitment to sustainability through its One Earth strategy.
'Working with clients like the National Gallery, which has a very strong commitment to sustainability, has pushed us as an organisation to find ways to be more responsible in the projects we deliver,' says Guaring. 'We recognise the work that we do impacts not only people and communities but also the planet.'
Ouroboros was commissioned to celebrate the National Gallery's 40th anniversary in 2022 and is due to be completed October 2024.